NVQ
QCF641 - Conforming to General Health, Safety and Welfare in the Workplace
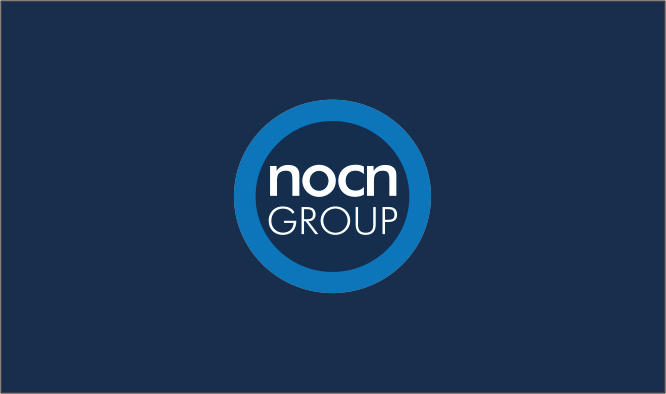
PFX+ | Featured Article
Unit 641 - 4.1 Demonstrate behaviour which shows personal responsibility for general workplace…
Unit 641 - 4.1 Demonstrate behaviour which shows personal responsibility for general workplace…
Demonstrate behaviour which shows personal responsibility for general workplace health, safety and welfare.
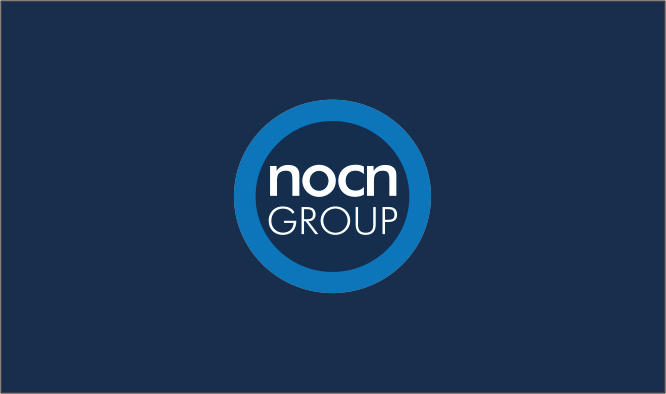
Unit 641 - 4.1 Demonstrate behaviour which shows personal responsibility for general workplace health, safety and welfare.
Demonstrate behaviour which shows personal responsibility for general workplace health, safety and welfare.
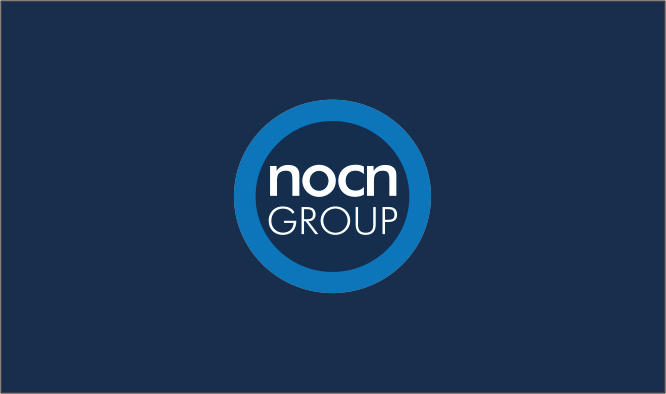
Showing personal responsibility for workplace health, safety, and welfare involves taking active steps to ensure your own safety and that of your colleagues in the workplace. This can be demonstrated through the following behaviors:
- Following health and safety procedures and protocols, such as wearing personal protective equipment, reporting hazards and incidents, and understanding emergency procedures.
- Taking care of your own well-being by maintaining good health, avoiding dangerous activities, and reporting any injuries or illnesses that occur at work.
- Reporting any safety concerns or hazards to the appropriate person or department, and actively participating in workplace safety meetings and training.
- Being aware of your own and others' behavior and ensuring that it does not pose a risk to health and safety.
- Keeping the work area clean, organized, and free of hazards, and using equipment and tools correctly and safely. Seeking out and taking advantage of opportunities for professional development in health and safety to stay informed about the latest best practices and regulations.
- Encouraging and supporting colleagues to adopt safe working practices and promoting a positive safety culture in the workplace.
By demonstrating these behaviors, individuals can take personal responsibility for their own and others' health, safety, and welfare in the workplace.
PFX+ | Featured Article
Unit 641 - 3.8 State how and when the different types of fire extinguishers are used in accordance…
Unit 641 - 3.8 State how and when the different types of fire extinguishers are used in accordance…
State how and when the different types of fire extinguishers are used in accordance with legislation and official guidance.
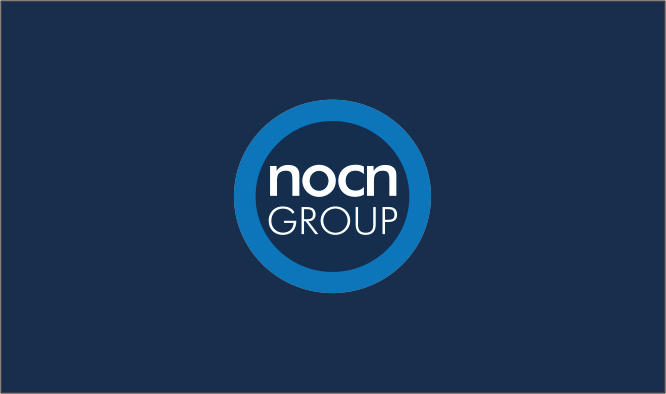
Unit 641 - 3.8 State how and when the different types of fire extinguishers are used in accordance with legislation and official guidance.
State how and when the different types of fire extinguishers are used in accordance with legislation and official guidance.
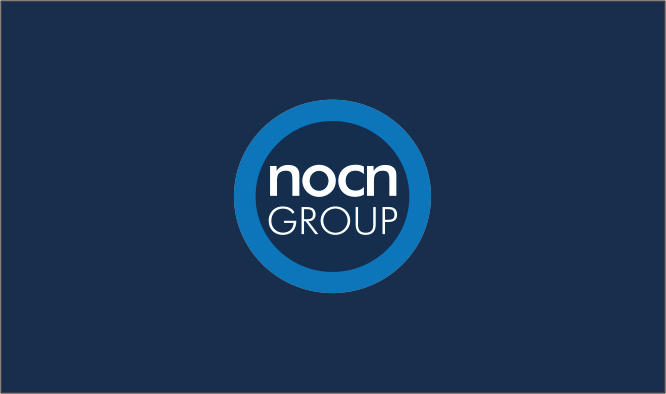
According to official guidance, the different types of fire extinguishers should be used in the following ways:
- Water Extinguishers: These are used for Class A fires (fires involving ordinary combustibles such as wood, paper, and cloth). They are not suitable for fires involving electrical equipment or flammable liquids.
- Foam Extinguishers: These are used for Class A and B fires (fires involving flammable liquids, gases, and electrical equipment). They are also suitable for some types of Class F fires (cooking oil and fat fires).
- Dry Powder Extinguishers: These are used for Class A, B, and C fires (fires involving flammable liquids, gases, electrical equipment, and live electrical apparatus).
- Carbon Dioxide Extinguishers: These are used for Class B and C fires (fires involving flammable liquids, gases, and electrical equipment). They are also suitable for some types of Class E fires (fires involving live electrical apparatus).
- Wet Chemical Extinguishers: These are used for Class F fires (cooking oil and fat fires).
In accordance with legislation, it is required to have the appropriate type of fire extinguisher in the workplace, and that all employees are trained on how to use them. The type and quantity of fire extinguishers required will depend on the size and nature of the workplace, and the type of fire hazards present.
The types of fire extinguishers and their uses are generally based on the classes of fires they are designed to extinguish. In the UK, fire safety legislation requires employers and business owners to ensure that the appropriate type of fire extinguisher is available and accessible in the workplace.
Here are the different types of fire extinguishers and their recommended uses:
- Water extinguishers (Class A fires): Suitable for fires involving wood, paper, textiles, and other Class A combustible materials. Not suitable for use on Class B (flammable liquids) or Class C (electrical) fires.
- Foam extinguishers (Class A and B fires): Suitable for Class A fires (wood, paper, textiles) and Class B fires (flammable liquids). Not suitable for use on Class C (electrical) fires.
- Powder extinguishers (Class A, B, and C fires): Suitable for Class A fires (wood, paper, textiles), Class B fires (flammable liquids), and Class C fires (electrical). They are also effective on some Class D (metal) fires.
- CO2 extinguishers (Class B and electrical fires): Suitable for Class B fires (flammable liquids) and electrical fires. Not suitable for use on Class A fires (wood, paper, textiles) or Class D (metal) fires.
- Wet chemical extinguishers (Class F fires): Suitable for fires involving cooking oils and fats, commonly found in commercial kitchens.
When using a fire extinguisher, it's important to follow the PASS technique:
- Pull the pin
- Aim the nozzle at the base of the fire
- Squeeze the handle
- Sweep the nozzle from side to side
It's also important to evacuate the area if the fire becomes too large or if you're unable to extinguish it. Call the emergency services and report the fire immediately.
Note: The specific regulations and guidance on fire extinguisher usage may vary depending on the country or region. It's important to refer to the appropriate legislation and official guidance in your area.
PFX+ | Featured Article
Unit 641 - 3.7 State the appropriate types of fire extinguishers relevant to the work.
Unit 641 - 3.7 State the appropriate types of fire extinguishers relevant to the work.
State the appropriate types of fire extinguishers relevant to the work.
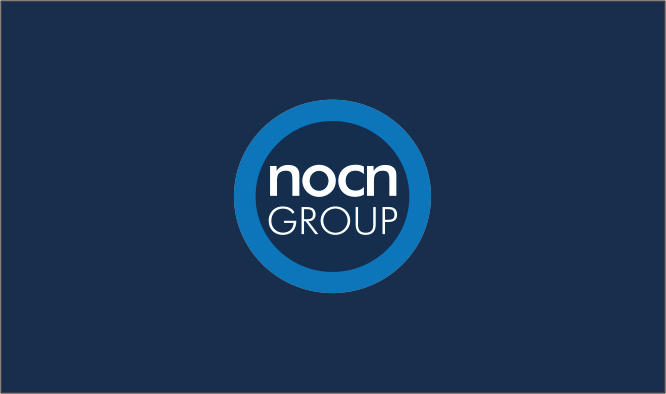
Unit 641 - 3.7 State the appropriate types of fire extinguishers relevant to the work.
State the appropriate types of fire extinguishers relevant to the work.
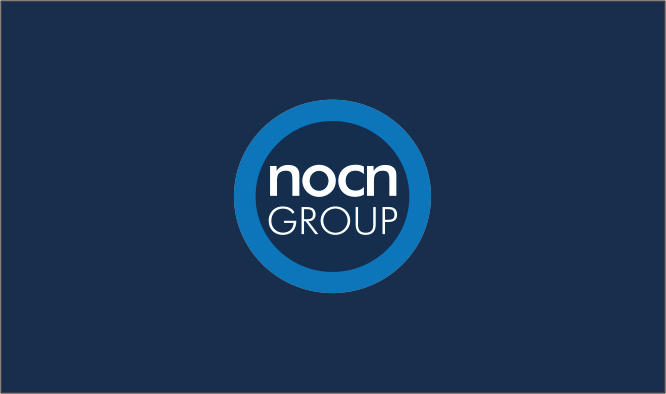
The appropriate type of fire extinguisher for plastering work would depend on the type of materials and fuels involved. In general, the most common types of fire extinguishers suitable for plastering work are:
- Water Fire Extinguishers: Suitable for Class A fires involving ordinary combustibles such as wood, paper, and textiles.
- Foam Fire Extinguishers: Suitable for Class A and Class B fires involving flammable liquids and gases.
- Dry Powder Fire Extinguishers: Suitable for Class A, Class B, and Class C fires involving flammable liquids, gases, and electrical equipment.
It is important to choose the right type of fire extinguisher for the type of fire that may occur and to ensure that employees are trained on how to use the extinguisher safely and effectively. In addition, it is important to regularly inspect and maintain fire extinguishers to ensure they are in good working order.
PFX+ | Featured Article
Unit 641 - 3.6 State the organisational policies and procedures for health, safety and welfare
Unit 641 - 3.6 State the organisational policies and procedures for health, safety and welfare
State the organisational policies and procedures for health, safety and welfare
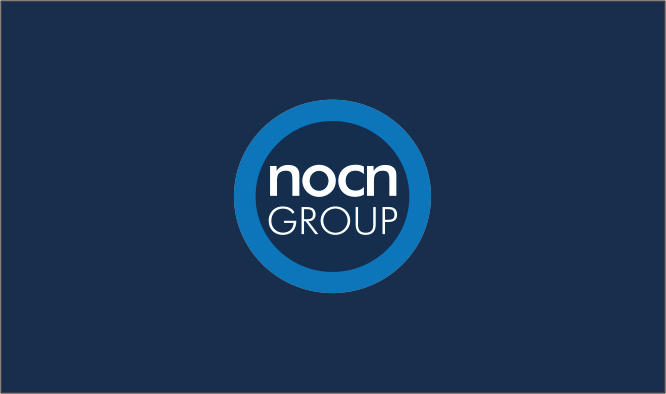
Unit 641 - 3.6 State the organisational policies and procedures for health, safety and welfare
State the organisational policies and procedures for health, safety and welfare
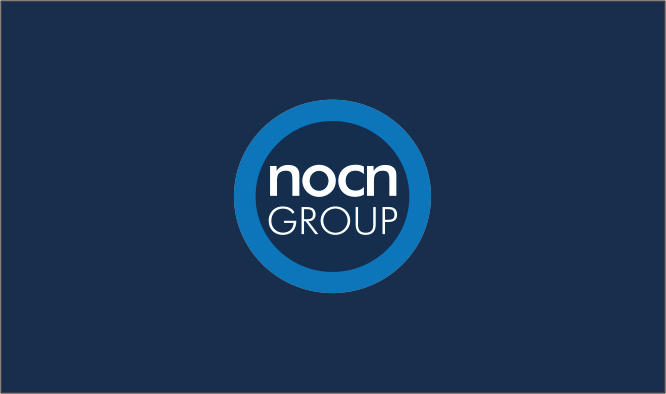
Organizational policies and procedures for health, safety, and welfare may include the following in relation to the listed topics:
- Dealing with accidents and emergencies associated with the work and environment: procedures for responding to accidents and emergencies, first aid provision, and emergency contact procedures.
- Methods of receiving or sourcing information: processes for obtaining information and training on health and safety issues, including relevant legislation and regulations.
- Reporting: procedures for reporting incidents, accidents, near misses, and hazardous conditions.
- Stopping work: processes for reporting and dealing with work that is considered to be dangerous or in breach of health and safety regulations.
- Evacuation: procedures for evacuation in case of fire or other emergencies, including fire drills.
- Fire risks and safe exit procedures: procedures for identifying and mitigating fire risks, including the provision of fire fighting equipment and fire exits.
- Consultation and feedback: procedures for seeking and receiving feedback and consultation from employees on health and safety issues, and for ensuring that their concerns are addressed.
It is important for employees to be familiar with these policies and procedures and to follow them in order to maintain a safe and healthy work environment.
PFX+ | Featured Article
Unit 641 - 3.5 Dispose of waste andor consumable items in accordance with legislation.
Unit 641 - 3.5 Dispose of waste andor consumable items in accordance with legislation.
Dispose of waste andor consumable items in accordance with legislation.
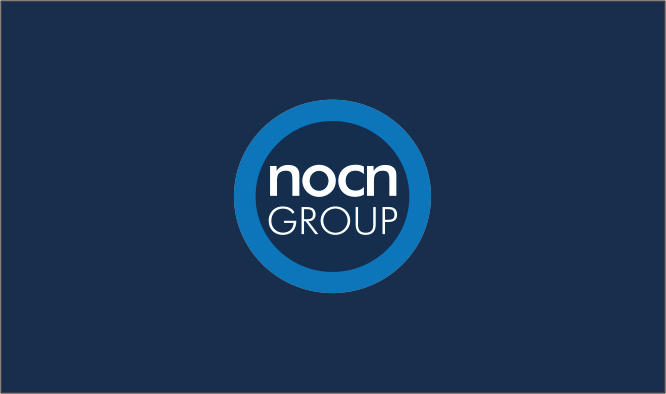
Unit 641 - 3.5 Dispose of waste andor consumable items in accordance with legislation.
Dispose of waste andor consumable items in accordance with legislation.
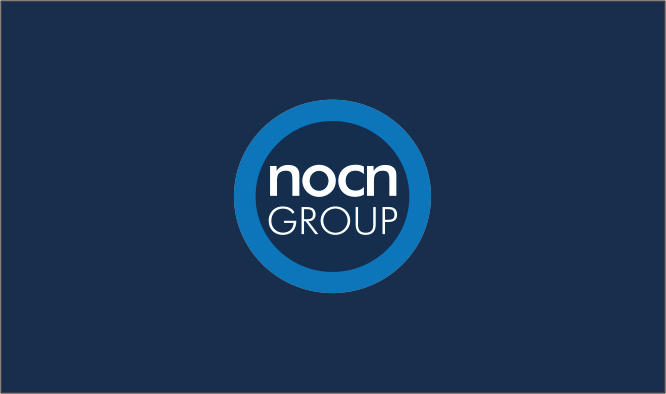
It is important to dispose of waste and consumable items in accordance with the applicable legislation. This helps ensure that the waste is managed in an environmentally responsible manner and protects human health and the environment. Failure to properly dispose of waste can result in harm to the environment and human health and may result in legal consequences.
PFX+ | Featured Article
Unit 641 - 3.4 Safely store health and safety control equipment in accordance with given…
Unit 641 - 3.4 Safely store health and safety control equipment in accordance with given…
Safely store health and safety control equipment in accordance with given instructions.
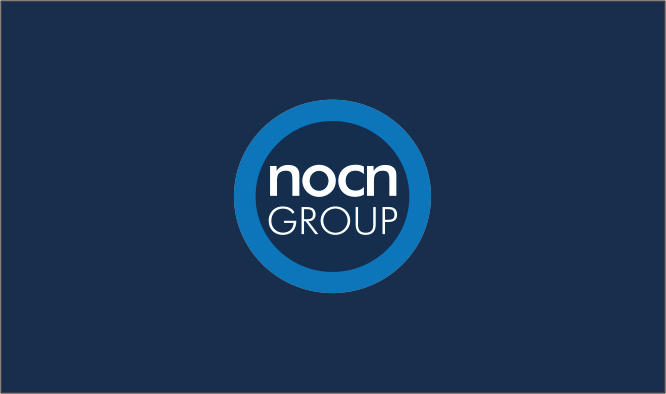
Unit 641 - 3.4 Safely store health and safety control equipment in accordance with given instructions.
Safely store health and safety control equipment in accordance with given instructions.
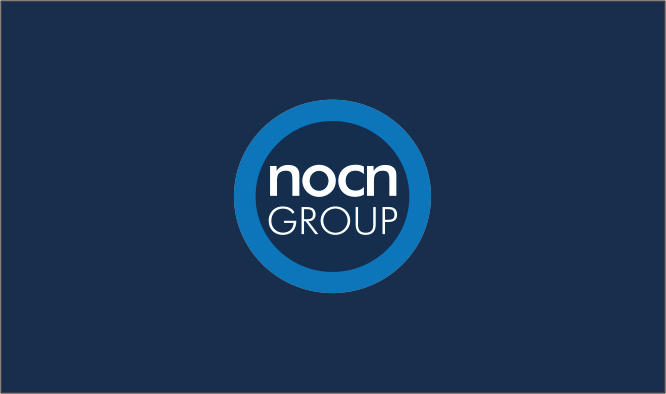
When plastering, it is important to store health and safety control equipment in a safe and secure manner, following the instructions provided. This can help ensure the equipment is properly maintained and readily accessible in case of an emergency.
Proper storage helps maintain the equipment's effectiveness and ensures that it is ready to use when needed.
PFX+ | Featured Article
Unit 641 - 3.3 Contribute to the maintenance of workplace welfare facilities in accordance with…
Unit 641 - 3.3 Contribute to the maintenance of workplace welfare facilities in accordance with…
Contribute to the maintenance of workplace welfare facilities in accordance with workplace welfare procedures.
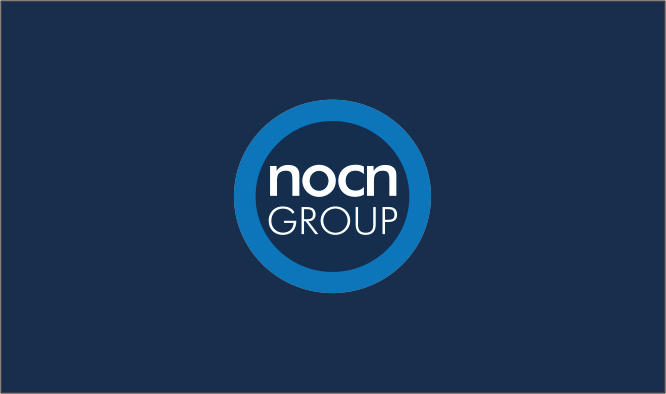
Unit 641 - 3.3 Contribute to the maintenance of workplace welfare facilities in accordance with workplace welfare procedures.
Contribute to the maintenance of workplace welfare facilities in accordance with workplace welfare procedures.
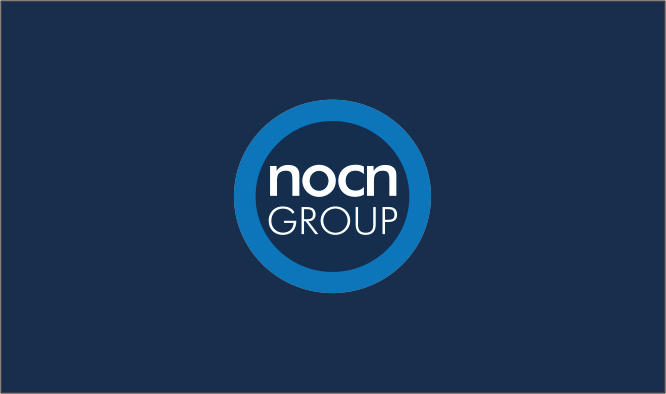
As a plasterer, it is important to understand the importance of maintaining workplace welfare facilities. Maintaining a safe and clean work environment not only benefits the workers, but also contributes to the overall efficiency of the work. To contribute to the maintenance of workplace welfare facilities, it is important to follow workplace welfare procedures carefully and consistently.
The first step in maintaining workplace welfare facilities is to ensure that they are regularly cleaned and kept in good condition. This may involve tasks such as cleaning toilets, showers, and changing rooms, as well as ensuring that they are supplied with necessary items such as soap, towels, and toilet paper.
In addition to regular cleaning, it is also important to carry out regular checks and maintenance tasks to ensure that the facilities are functioning properly. This may involve checking plumbing and electrical systems, fixing any leaks or damage, and replacing any broken or worn out equipment.
It is also important to follow health and safety procedures when using workplace welfare facilities. This may involve following guidelines for using equipment such as showers, as well as taking measures to prevent the spread of disease, such as washing hands frequently and covering cuts and wounds.
Finally, it is important to report any issues or concerns regarding workplace welfare facilities to the appropriate person. This may involve reporting any damage or safety hazards, as well as making suggestions for improvements.
In conclusion, as a plasterer, it is important to contribute to the maintenance of workplace welfare facilities in order to ensure that they are clean, safe, and functioning properly. By following workplace welfare procedures and reporting any issues or concerns, plasterers can help to maintain a safe and efficient work environment for themselves and their colleagues.
PFX+ | Featured Article
Unit 641 - 3.2 Contribute to discussions by offeringproviding feedback relating to health, safety…
Unit 641 - 3.2 Contribute to discussions by offeringproviding feedback relating to health, safety…
Contribute to discussions by offeringproviding feedback relating to health, safety and welfare.
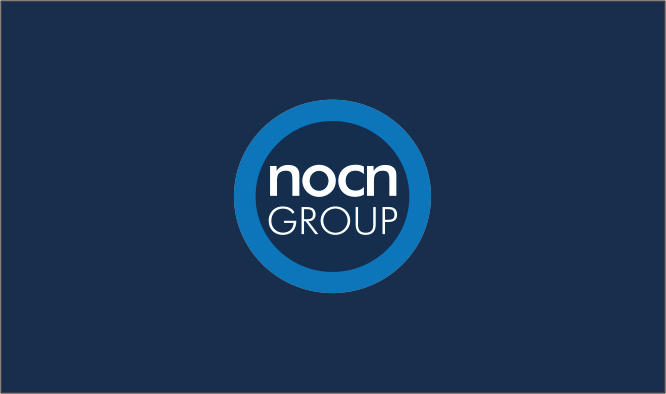
Unit 641 - 3.2 Contribute to discussions by offeringproviding feedback relating to health, safety and welfare.
Contribute to discussions by offeringproviding feedback relating to health, safety and welfare.
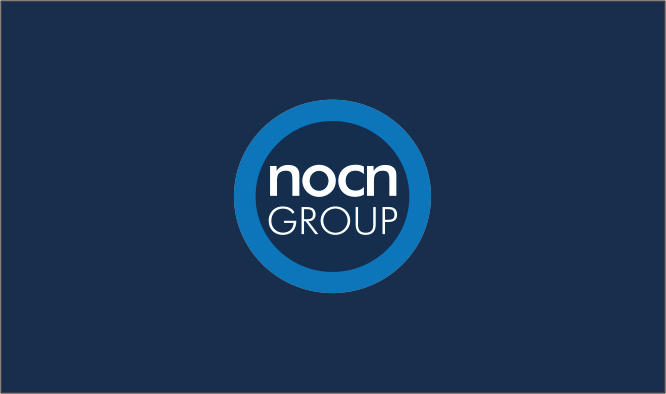
Health, safety, and welfare are crucial topics and ensuring their promotion should be a priority in any discussion or decision-making process.
When it comes to health, it's important to consider the physical and mental well-being of individuals. This can include access to proper healthcare, healthy working and living conditions, and promoting healthy lifestyles.
In terms of safety, it's important to consider measures that minimize risks and prevent accidents in various settings, such as the workplace, home, and public spaces. This can involve adhering to safety regulations, providing proper training and equipment, and conducting regular safety assessments.
Regarding welfare, it's important to ensure that basic needs are met and that individuals are able to live a fulfilling life. This can include access to adequate housing, food, and financial security, as well as support for mental health and personal development.
In summary, when offering feedback relating to health, safety, and welfare, it's important to consider the overall well-being of individuals and the steps that can be taken to promote and protect it.
PFX+ | Featured Article
Unit 641 - 3.1 Interpret and comply with given instructions to maintain safe systems of work and…
Unit 641 - 3.1 Interpret and comply with given instructions to maintain safe systems of work and…
Interpret and comply with given instructions to maintain safe systems of work and quality working practices.
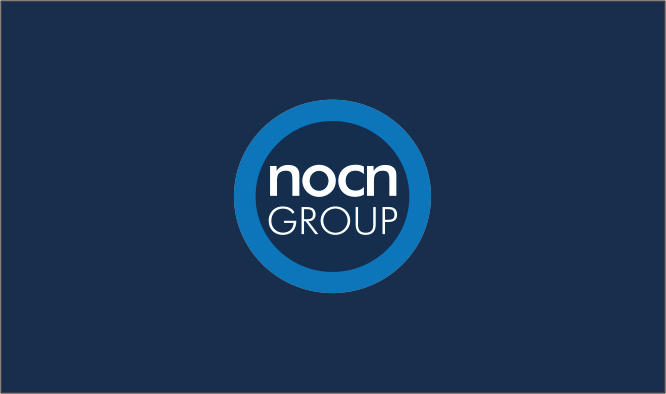
Unit 641 - 3.1 Interpret and comply with given instructions to maintain safe systems of work and quality working practices.
Interpret and comply with given instructions to maintain safe systems of work and quality working practices.
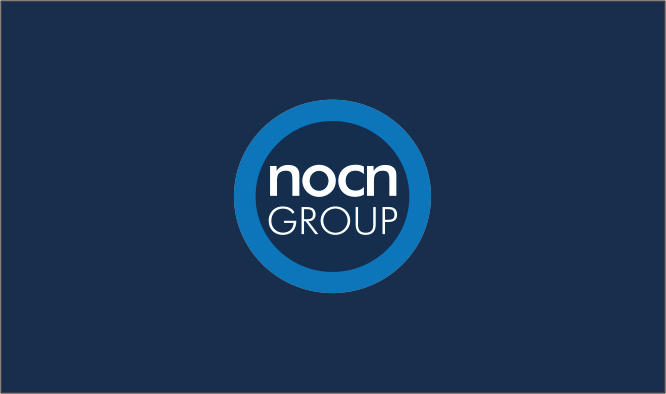
Interpreting and complying with instructions to maintain safe systems of work and quality working practices involves several steps:
- Understanding the instructions: It's important to take the time to read and understand the instructions thoroughly, asking for clarification if needed. This includes both written instructions, such as safety procedures and guidelines, as well as verbal instructions given by supervisors or trainers.
- Following the instructions: Once the instructions are understood, they should be followed closely and consistently. This includes following safe systems of work and quality working practices, such as wearing personal protective equipment (PPE), using equipment correctly, and following proper procedures for handling hazardous substances.
- Monitoring compliance: Regular monitoring is important to ensure that instructions are being followed correctly and that safe systems of work and quality working practices are being maintained. This can be done through regular inspections, safety audits, and feedback from employees.
- Taking corrective action: If deviations from the instructions are identified, prompt corrective action should be taken to bring practices back into compliance. This may include additional training for employees, changes to procedures or equipment, or the implementation of new controls to mitigate risks.
- Continual improvement: Regularly reviewing and updating instructions, procedures, and processes can help to maintain safe systems of work and quality working practices over time. This can be done through regular safety assessments, feedback from employees, and incorporating best practices from other organizations.
By following these steps, individuals can help to maintain a safe and healthy work environment, reduce the risk of accidents and injuries, and promote quality working practices.
PFX+ | Featured Article
Unit 641 - 2.6 State the methods used for reporting changed circumstances, hazards and incidents in…
Unit 641 - 2.6 State the methods used for reporting changed circumstances, hazards and incidents in…
State the methods used for reporting changed circumstances, hazards and incidents in the workplace.
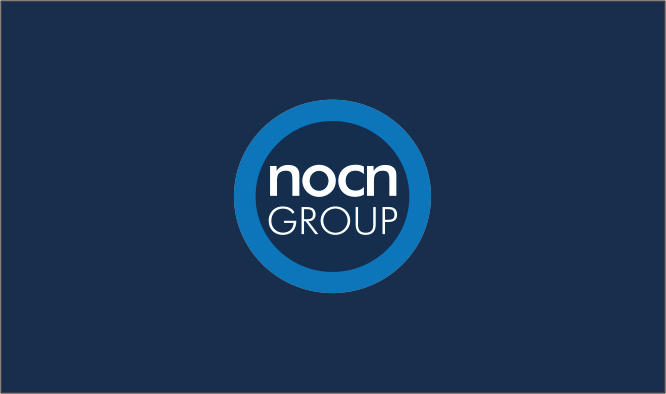
Unit 641 - 2.6 State the methods used for reporting changed circumstances, hazards and incidents in the workplace.
State the methods used for reporting changed circumstances, hazards and incidents in the workplace.
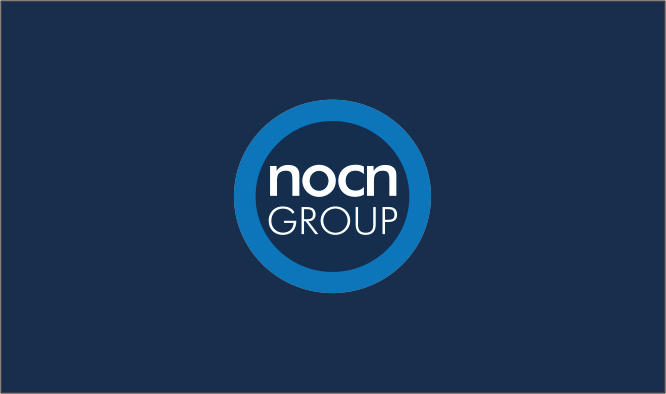
The methods used for reporting changed circumstances, hazards, and incidents in the workplace can vary depending on the specific workplace, but some common methods include:
- Incident reporting forms: Many workplaces have standardized forms that employees can fill out to report incidents, hazards, or changed circumstances.
- Oral reporting: In some workplaces, employees may be encouraged to report hazards, incidents, or changed circumstances directly to their supervisor or safety representative.
- Online reporting: Some workplaces may have an online reporting system that employees can use to report hazards, incidents, or changed circumstances.
- Anonymous reporting: In some cases, employees may be able to report hazards, incidents, or changed circumstances anonymously, either through a designated reporting mechanism or through a third-party hotline.
- Employee suggestion programs: Some workplaces may have an employee suggestion program that allows employees to provide feedback and suggest improvements, including reporting hazards, incidents, or changed circumstances.
Regardless of the specific method used, it's important for employers to establish a clear and effective reporting system that allows employees to report hazards, incidents, and changed circumstances quickly and easily. This can help to ensure that workplace hazards are identified and addressed in a timely manner, and can help to prevent accidents and injuries.
PFX+ | Featured Article
Unit 641 - 2.5 State how changing circumstances within the workplace could cause hazards.
Unit 641 - 2.5 State how changing circumstances within the workplace could cause hazards.
State how changing circumstances within the workplace could cause hazards.
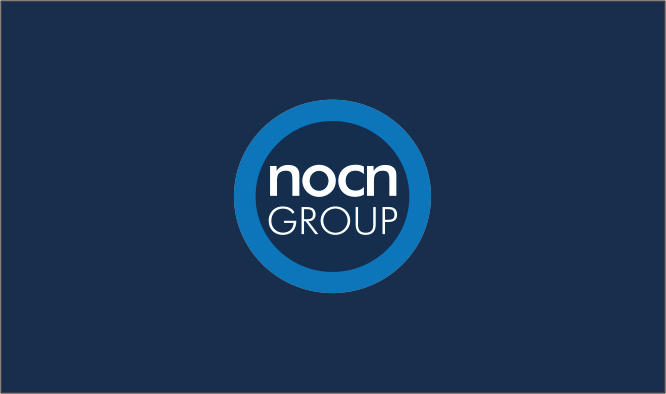
Unit 641 - 2.5 State how changing circumstances within the workplace could cause hazards.
State how changing circumstances within the workplace could cause hazards.
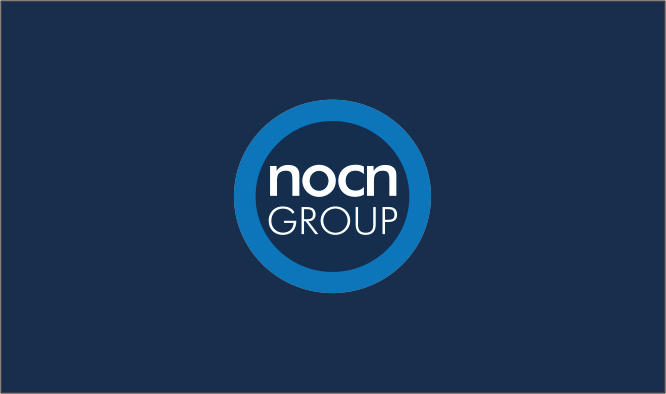
There are many different circumstances within the workplace that can change and create new hazards. Some examples include:
- Workload changes: An increase in workload, or the introduction of new tasks, can lead to increased physical or mental stress on workers.
- New equipment or technology: The introduction of new equipment or technology can create new hazards, such as exposure to hazardous substances or increased risk of electrical shock.
- Changes in the physical work environment: Changes in the physical work environment, such as the addition of new structures or the removal of protective barriers, can increase the risk of falls, trips, and other physical hazards.
- Changes in staffing: Changes in staffing, such as the loss of experienced workers or the addition of new workers, can lead to increased risk of accidents or injuries.
- Changes in weather or natural conditions: Changes in weather or natural conditions, such as extreme heat or cold, heavy rain or snow, or increased risk of fire or flooding, can create new hazards for workers.
It is important for employers to be aware of changing circumstances within the workplace and to assess and address any new hazards that may arise. This can help to ensure a safe and healthy work environment for all employees.
PFX+ | Featured Article
Unit 641 - 2.4 List the current Health and Safety Executive top five health risks.
Unit 641 - 2.4 List the current Health and Safety Executive top five health risks.
List the current Health and Safety Executive top five health risks.
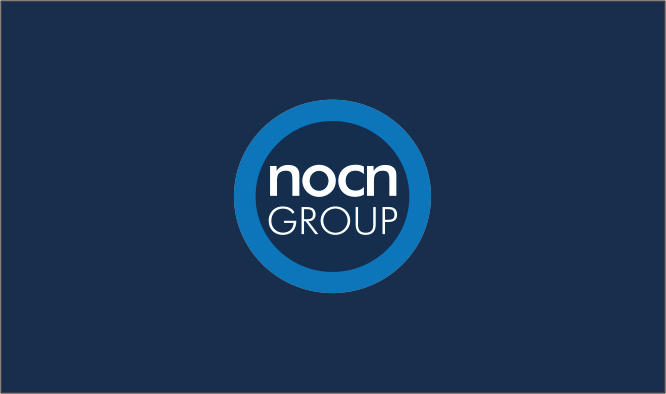
Unit 641 - 2.4 List the current Health and Safety Executive top five health risks.
List the current Health and Safety Executive top five health risks.
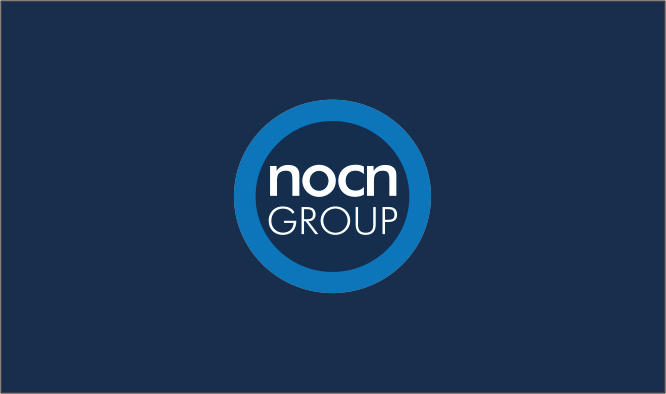
PFX+ | Featured Article
Unit 641 - 2.3 List the current Health and Safety Executive top ten safety risks.
Unit 641 - 2.3 List the current Health and Safety Executive top ten safety risks.
List the current Health and Safety Executive top ten safety risks.
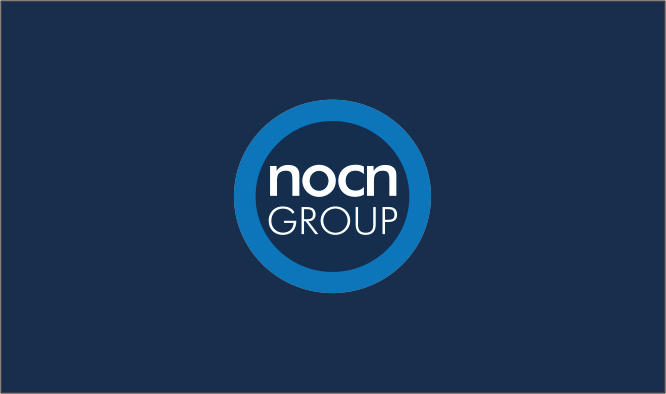
Unit 641 - 2.3 List the current Health and Safety Executive top ten safety risks.
List the current Health and Safety Executive top ten safety risks.
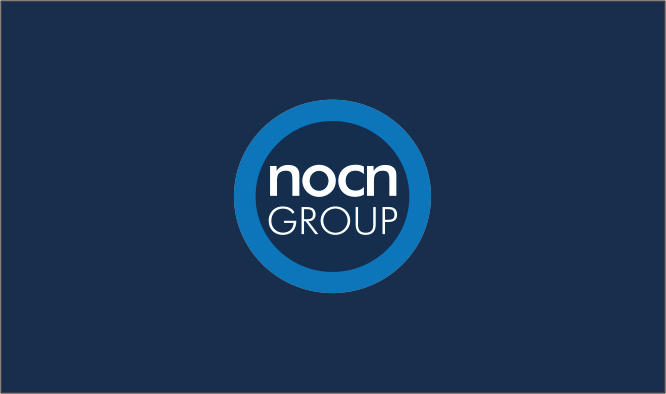
- Falls from heig
- Being struck by a moving vehic
- Slips, trips, and falls on the same lev
- Manual handli
- Work-related stress, violence, and bullyi
- Working with asbest
- Noise-induced hearing lo
- Hand-arm vibration syndrome (HAV)
- Respiratory diseases from inhaling hazardous substanc
- Skin diseases caused by exposure to hazardous substances or poor hand hygien.
It's important for employers to regularly assess their workplace for these and other hazards and to take appropriate action to minimize risk and protect workers.
PFX+ | Featured Article
Unit 641 - 2.2 List typical hazards associated with the work environment and occupational area in…
Unit 641 - 2.2 List typical hazards associated with the work environment and occupational area in…
List typical hazards associated with the work environment and occupational area in relation to resources, substances, asbestos, equipment, obstructions, storage, services and work
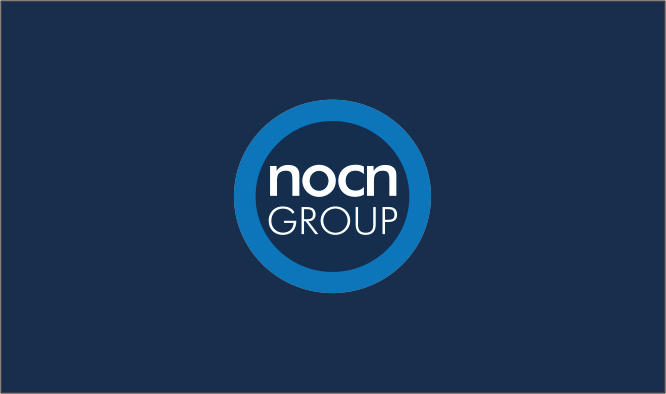
Unit 641 - 2.2 List typical hazards associated with the work environment and occupational area in relation to resources, substances, asbestos, equipment, obstructions, storage, ser
List typical hazards associated with the work environment and occupational area in relation to resources, substances, asbestos, equipment, obstructions, storage, services and work
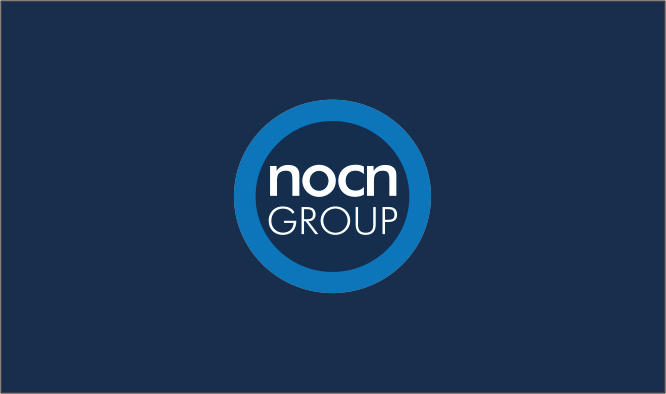
Here is a list of typical hazards associated with the work environment and occupational area in relation to plastering:
Resources:
- Lack of protective equipment such as gloves, masks, or safety glasses
Substances:
- Inhalation of dust or particulate matter from plaster, joint compound, or other materials
- Skin irritation or allergic reactions from contact with plaster or other substances
Asbestos:
- Inhalation of asbestos fibers that may be present in older buildings
Equipment:
- Mechanical hazards from power tools or equipment such as power sanders or mixers
- Electrocution from electrical equipment or power lines
Obstructions:
- Trips, slips, and falls from cluttered or obstructed work areas or walkways
Storage:
- Injuries from collapsing or unstable storage piles or containers
Services:
- Poor ventilation, lighting, or heating that can contribute to a hazardous work environment
Work activities:
- Strain injuries from heavy lifting or manual labor
- Repetitive motion injuries from repetitive tasks
- Injuries from working at heights, such as when installing or repairing ceilings
It's important for employers and workers in the plastering industry to be aware of these and other hazards, and to take appropriate safety measures to prevent injuries and maintain a safe work environment.
PFX+ | Featured Article
Unit 641 - 2.1 Report any hazards created by changing circumstances within the workplace in…
Unit 641 - 2.1 Report any hazards created by changing circumstances within the workplace in…
Report any hazards created by changing circumstances within the workplace in accordance with organisational procedures.
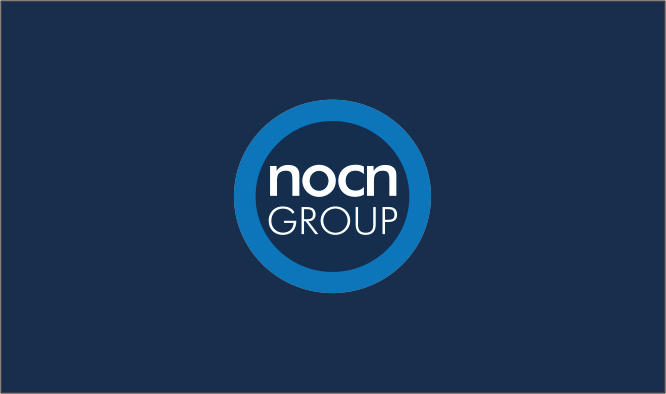
Unit 641 - 2.1 Report any hazards created by changing circumstances within the workplace in accordance with organisational procedures.
Report any hazards created by changing circumstances within the workplace in accordance with organisational procedures.
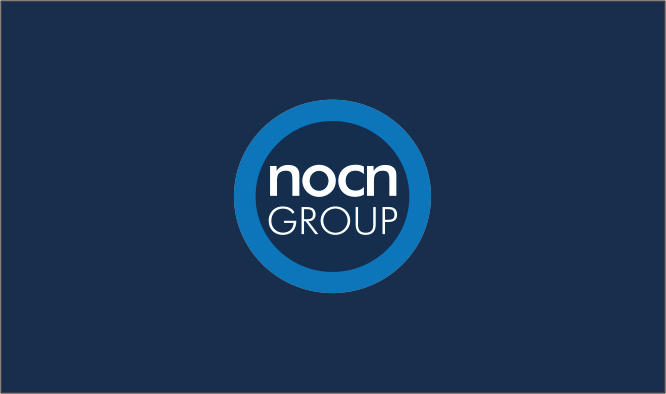
To report any hazards created by changing circumstances within the workplace, you should follow these steps:
- Observe and identify the hazard: Be vigilant and aware of any changes in the workplace that could create a hazard, such as new equipment or materials, changes in work processes, or environmental factors.
- Assess the risk: Evaluate the potential harm that the hazard could cause, such as injury to workers or damage to equipment. Report the hazard: Report the hazard to the appropriate person, such as a supervisor or health and safety representative, following the procedures set out by your organization.
- Document the report: Make a written record of the hazard and the steps taken to report it, including the date, time, and the name of the person you reported it to.
- Take corrective action: Depending on the severity of the hazard, corrective action may need to be taken immediately to remove or mitigate the risk. Your organization may have procedures for this.
By following these steps, you can help to ensure that hazards created by changing circumstances within the workplace are identified, reported, and addressed in a timely and effective manner, in accordance with organizational procedures.
PFX+ | Featured Article
Unit 641 - 1.8 State how to comply with control measures that have been identified by risk…
Unit 641 - 1.8 State how to comply with control measures that have been identified by risk…
State how to comply with control measures that have been identified by risk assessments and safe systems of work.
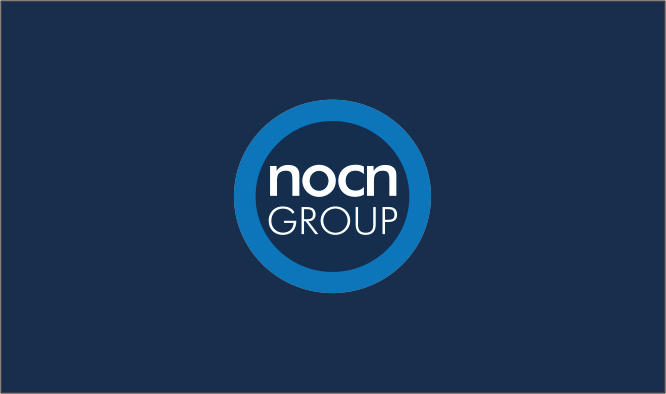
Unit 641 - 1.8 State how to comply with control measures that have been identified by risk assessments and safe systems of work.
State how to comply with control measures that have been identified by risk assessments and safe systems of work.
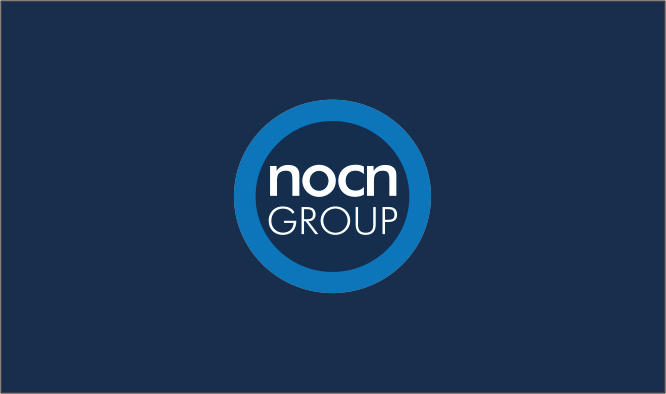
To comply with control measures identified by risk assessments and safe systems of work, one must follow these steps:
- Familiarize yourself with the control measures: Read and understand the risk assessments and safe systems of work that have been put in place for your job or workplace.
- Implement the control measures: Ensure that all control measures are put into practice, such as using personal protective equipment, following safe operating procedures, and adhering to any warnings or notices.
- Regularly review the control measures: Ensure that the control measures are still relevant and effective. If necessary, make changes to ensure that they continue to provide adequate protection.
- Provide training and information: Ensure that all workers and contractors are aware of the control measures and understand how to comply with them.
- Report any incidents or near misses: If an incident or near miss occurs, report it immediately and take action to prevent similar incidents in the future.
By following these steps, you can help to ensure that you are complying with the control measures identified by risk assessments and safe systems of work, which will help to maintain a safe and healthy working environment.
PFX+ | Featured Article
Unit 641 - 1.7 State why health, safety and welfare legislation, notices and warning signs are…
Unit 641 - 1.7 State why health, safety and welfare legislation, notices and warning signs are…
State why health, safety and welfare legislation, notices and warning signs are relevant to the occupational area.
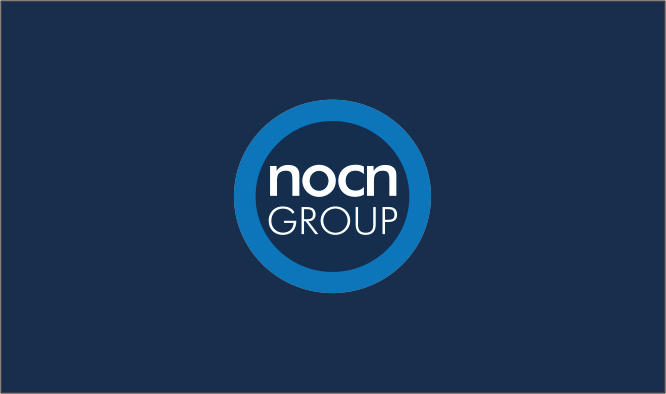
Unit 641 - 1.7 State why health, safety and welfare legislation, notices and warning signs are relevant to the occupational area.
State why health, safety and welfare legislation, notices and warning signs are relevant to the occupational area.
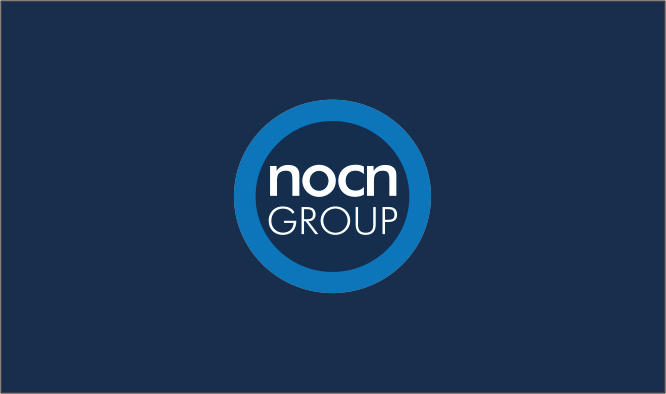
Health, safety, and welfare legislation, notices, and warning signs are relevant to the occupational area because they help to create a safe and secure working environment and prevent accidents, injuries, and illnesses in the workplace. These measures are designed to protect the health and safety of workers and others who may be affected by the work being carried out. Additionally, following these regulations helps to meet legal requirements and avoid potential liabilities for employers and employees. Overall, these measures help to ensure that work is performed safely and responsibly, creating a healthier and more secure work environment for everyone involved.
PFX+ | Featured Article
Unit 641 - 1.6 State which types of health, safety and welfare legislation, notices and warning…
Unit 641 - 1.6 State which types of health, safety and welfare legislation, notices and warning…
State which types of health, safety and welfare legislation, notices and warning signs are relevant to the occupational area and associated equipment.
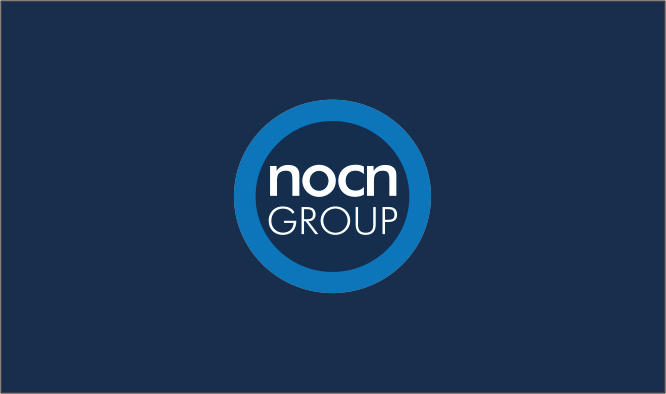
Unit 641 - 1.6 State which types of health, safety and welfare legislation, notices and warning signs are relevant to the occupational area and associated equipment.
State which types of health, safety and welfare legislation, notices and warning signs are relevant to the occupational area and associated equipment.
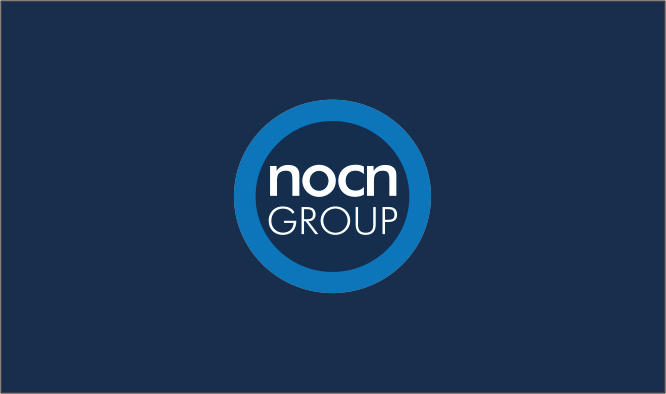
Health and safety legislation relevant to the plastering NVQ occupational area and associated equipment include:
- The Health and Safety at Work Act 1974
- The Management of Health and Safety at Work Regulations 1999
- The Construction (Design and Management) Regulations 2015
- The Control of Substances Hazardous to Health Regulations 2002 (COSHH)
- The Provision and Use of Work Equipment Regulations 1998 (PUWER)
Welfare legislation relevant to the plastering NVQ occupational area and associated equipment include:
- The Workplace (Health, Safety and Welfare) Regulations 1992
- The Personal Protective Equipment at Work Regulations 1992
Warning signs and notices to be displayed in the plastering occupational area include:
- Fire exit signs
- First aid signs
- Hazard warning signs for specific equipment or substances
- Safety signs for personal protective equipment (PPE) requirements
- Signs for emergency procedures and evacuation routes.
It's important to comply with relevant legislation and display appropriate signs to ensure the health, safety, and welfare of workers and other people who may be affected by the work activities.
PFX+ | Featured Article
Unit 641 - 1.5 State how the health and safety control equipment relevant to the work should be used…
Unit 641 - 1.5 State how the health and safety control equipment relevant to the work should be used…
State how the health and safety control equipment relevant to the work should be used in accordance with the given instructions.
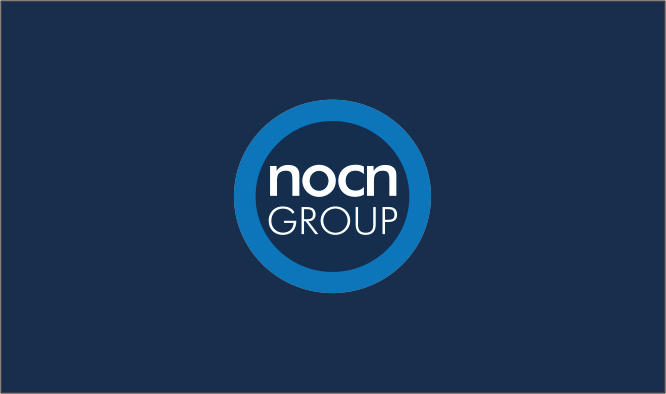
Unit 641 - 1.5 State how the health and safety control equipment relevant to the work should be used in accordance with the given instructions.
State how the health and safety control equipment relevant to the work should be used in accordance with the given instructions.
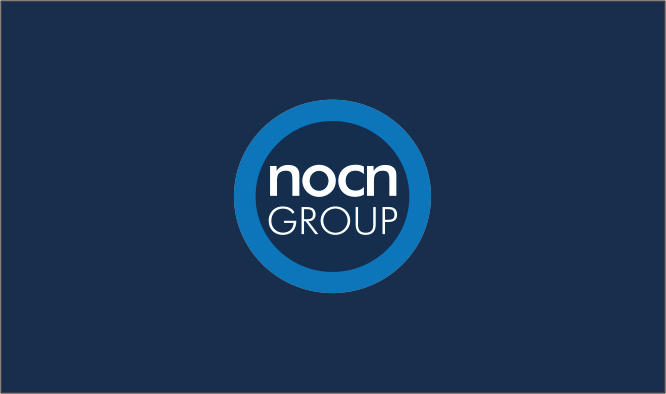
The health and safety control equipment relevant to the work should be used in accordance with the given instructions to ensure the safe and effective use of the equipment. The following steps should be taken:
- Read the instructions and become familiar with the equipment and its intended use.
- Ensure that the equipment is in good working condition before use and report any faults to your supervisor.
- Follow the manufacturer's instructions and industry standards when using the equipment.
- Wear appropriate protective equipment when using the equipment.
- Set up the equipment in a safe and stable position in a clear work area.
- Use the equipment in accordance with relevant health and safety legislation and the requirements of your organization.
- Regularly inspect the equipment and perform maintenance as necessary to keep it in good working order.
- Dispose of equipment that is no longer usable in accordance with the instructions and relevant regulations.
By following the instructions and using the equipment correctly, individuals can help ensure the safe and effective use of the equipment and minimize the risk of accidents and injuries.
PFX+ | Featured Article
Unit 641 - 1.4 State why and when health and safety control equipment, identified by the principles…
Unit 641 - 1.4 State why and when health and safety control equipment, identified by the principles…
State why and when health and safety control equipment, identified by the principles of protection, should be used relating to types, purpose and limitations of each type, the work situation, occupational use a
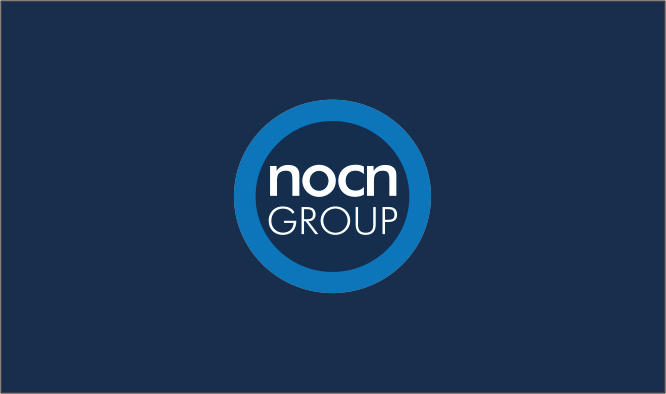
Unit 641 - 1.4 State why and when health and safety control equipment, identified by the principles of protection, should be used relating to types, purpose and limitations of each
State why and when health and safety control equipment, identified by the principles of protection, should be used relating to types, purpose and limitations of each type, the work situation, occupational use a
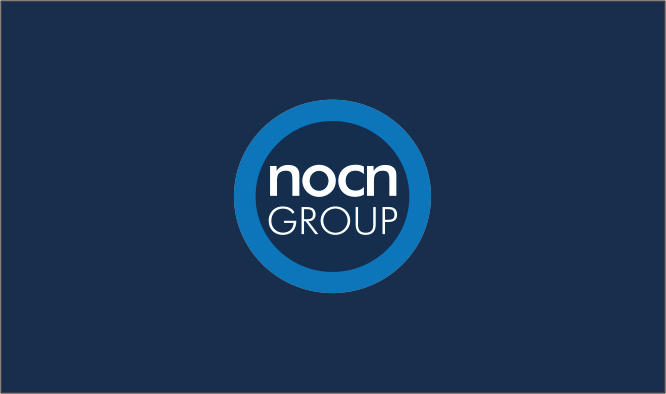
Health and safety control equipment should be used in relation to plastering to prevent accidents and illnesses that may result from exposure to hazardous materials and dangerous working conditions. The use of such equipment is determined by the principles of protection, which include collective protective measures, personal protective equipment (PPE), respiratory protective equipment (RPE), and local exhaust ventilation (LEV).
Collective protective measures are measures that are put in place to protect workers as a whole and include, for example, installing ventilation systems, enclosing machinery, and providing adequate lighting.
Personal protective equipment (PPE) is equipment that is worn by an individual to protect them from hazardous substances, for example, gloves, face shields, and protective clothing. PPE should be selected based on the type and nature of the hazard, the duration of exposure, and the user's comfort and mobility.
Respiratory protective equipment (RPE) is used to protect individuals from breathing in hazardous substances and includes respirators, face masks, and air-purifying respirators. RPE should be selected based on the type and concentration of the substance, the duration of exposure, and the user's comfort and mobility.
Local exhaust ventilation (LEV) is a type of ventilation system that is used to remove hazardous substances from the immediate area of work. LEV is used to control the exposure of workers to hazardous substances and should be selected based on the type and concentration of the substance, the duration of exposure, and the type of work being carried out.
In conclusion, health and safety control equipment should be used in relation to plastering to protect individuals from hazardous substances and dangerous working conditions. The type and use of such equipment should be based on the principles of protection and the work situation, including the type and concentration of the substance, the duration of exposure, and the user's comfort and mobility.
PFX+ | Featured Article
Unit 641 - 1.3 Comply with statutory requirements, safety notices and warning notices displayed…
Unit 641 - 1.3 Comply with statutory requirements, safety notices and warning notices displayed…
Comply with statutory requirements, safety notices and warning notices displayed within the workplace andor on equipment.
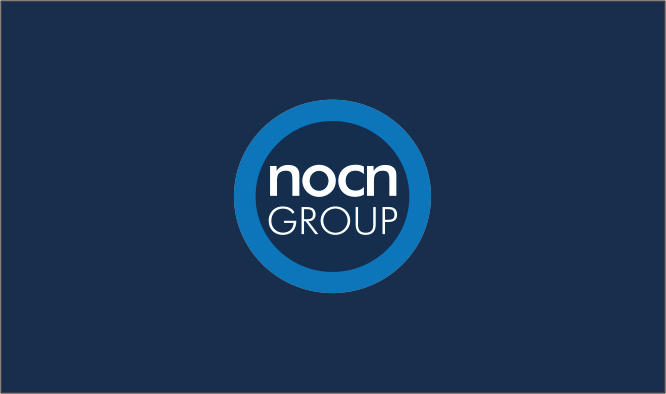
Unit 641 - 1.3 Comply with statutory requirements, safety notices and warning notices displayed within the workplace andor on equipment.
Comply with statutory requirements, safety notices and warning notices displayed within the workplace andor on equipment.
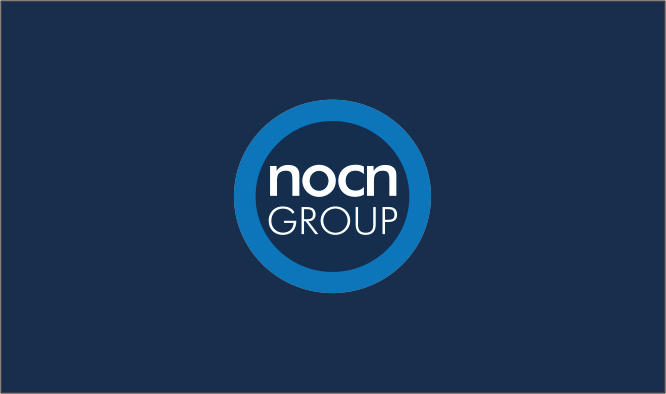
To comply with statutory requirements, safety notices, and warning notices in the workplace while carrying out plastering activities as part of an NVQ, it is recommended to follow these steps:
- Read and understand all notices and warning signs posted in the workplace and on equipment.
- Follow the instructions provided in the notices and take the necessary precautions. Familiarize yourself with relevant health and safety legislation and the requirements of your organization.
- Report any damaged or missing notices to your supervisor.
- Keep yourself informed of any updates or changes to the notices and follow any new instructions.
By following these steps, you can help ensure that you are complying with all relevant statutory requirements, safety notices, and warning notices in the workplace, which will help to maintain a safe working environment for everyone involved in the plastering activities.
PFX+ | Featured Article
Unit 641 - 1.2 Use health and safety control equipment safely to carry out the activity in…
Unit 641 - 1.2 Use health and safety control equipment safely to carry out the activity in…
Use health and safety control equipment safely to carry out the activity in accordance with legislation and organisational requirements.
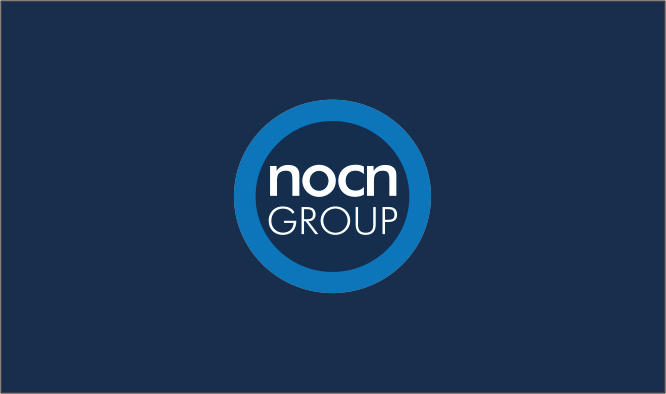
Unit 641 - 1.2 Use health and safety control equipment safely to carry out the activity in accordance with legislation and organisational requirements.
Use health and safety control equipment safely to carry out the activity in accordance with legislation and organisational requirements.
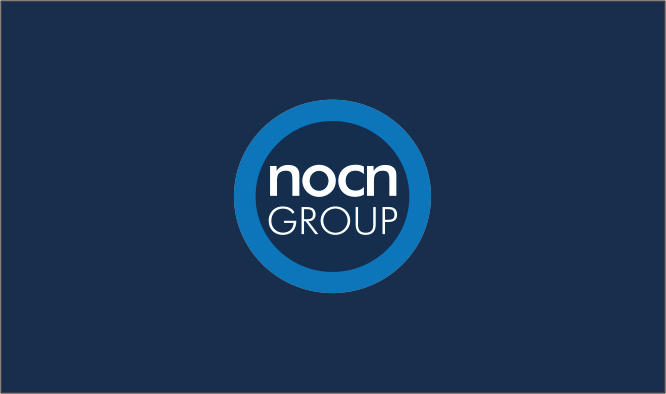
To use health and safety control equipment safely while carrying out plastering activities, it is recommended to follow these steps:
- Familiarize yourself with the equipment and its intended use. Read the manual or receive training from a knowledgeable person.
- Ensure that the equipment is in good working condition before use and report any faults to your supervisor. Use the equipment in accordance with the manufacturer's instructions and industry standards.
- Follow all relevant health and safety legislation, such as OSHA standards, and the requirements of your organization.
- Always wear appropriate protective equipment when using the equipment. Make sure that the work area is clear of any potential hazards and that the equipment is set up in a safe and stable position.
- Regularly inspect the equipment and perform maintenance as necessary to keep it in good working order.
By following these steps, you can help ensure the safe and effective use of health and safety control equipment while carrying out plastering activities.
PFX+ | Featured Article
Unit 641 - 1.1 Comply with information and workplace inductions and any health, safety and welfare…
Unit 641 - 1.1 Comply with information and workplace inductions and any health, safety and welfare…
Comply with information and workplace inductions and any health, safety and welfare briefings attended relevant to the occupational area.
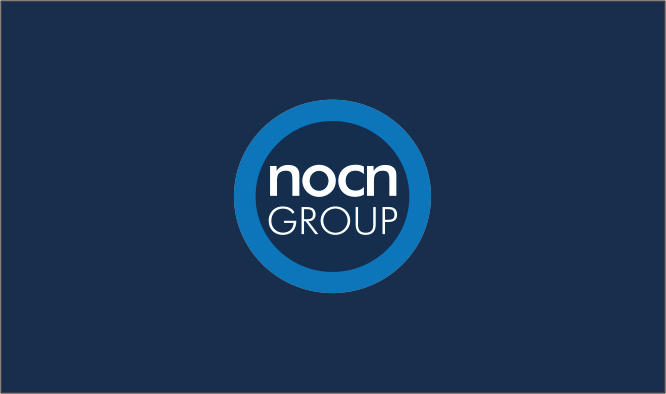
Unit 641 - 1.1 Comply with information and workplace inductions and any health, safety and welfare briefings attended relevant to the occupational area.
Comply with information and workplace inductions and any health, safety and welfare briefings attended relevant to the occupational area.
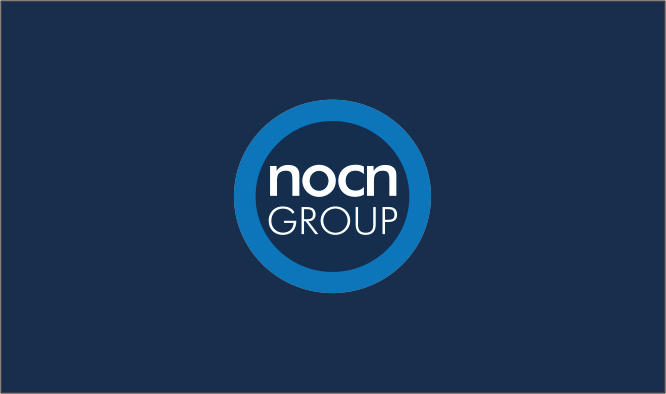
In the context of plastering, complying with information from workplace inductions and health, safety, and welfare briefings is essential for ensuring the safety of individuals working in this field. These inductions and briefings provide important information on the specific health, safety, and welfare requirements of the workplace, and are designed to help individuals understand and follow the relevant guidelines and procedure
For example, individuals may be briefed on the proper use of tools and equipment, the hazards associated with different materials and substances used in plastering, and the measures that must be taken to prevent accidents and injuries. They may also be provided with information on emergency procedures and the procedures for reporting incidents and accident
It is important that individuals take this information seriously and comply with the guidelines and procedures outlined in the workplace inductions and health, safety, and welfare briefings. Failure to do so can result in accidents, injuries, and other safety incidents, which can have serious consequences for both the individual and the workplace. By complying with the information from workplace inductions and health, safety, and welfare briefings, individuals can ensure that they are working in a safe and responsible manner, and are contributing to the overall health and safety of the workplace